Case Study - Design of Experiments - Energy Efficiency Products
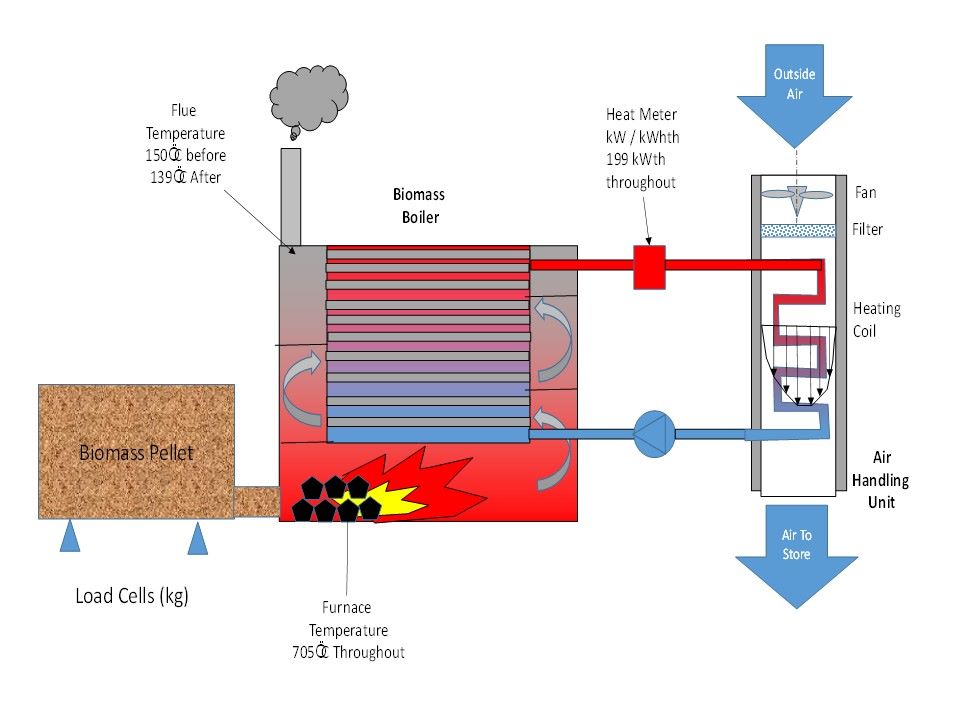
The claim of this product is that improves thermal efficiency - useful heat out divided by fuel in measured in kWh. It was decided to test this on Biomass boilers because it was possible to reliably measure fuel in from load cells, heat out from heater meters used for RHI purposes, plus furnace, flue and AHU temperatures. The first trial was done on four boilers over six days - three days before the energy product was added and three days after.
This was done in this way so that all conditions - boiler operations, ambient weather and heating loads were more or less constant. What was noted was that there was an increase in thermal efficiency of about 5% (more heat out vs fuel in), and that the temperature of the flue gas dropped about 15°C.
The trial was then rolled out to a further 10 boilers with similar results - average efficiency increase 7.5%. Based on this a full roll out occurred over 90 boilers and was assessed over four winter months (Jan to April).
The payback of using this product was estimated at about 12 months
assuming a 5% improvement.
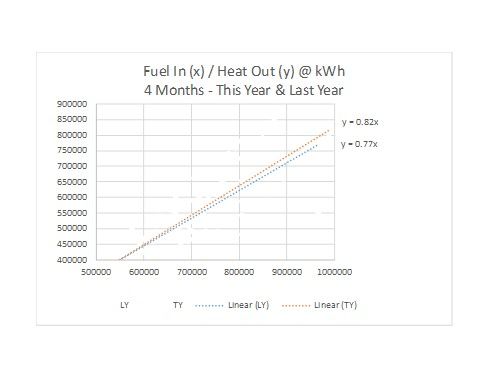
Measuring results over four winter months, other factors come into play such as:-
- Difference in weather patterns,
- fuel measurement accuracy after multiple fills of the fuel hopper,
- maintenance of the boilers (i.e. efficiency may increase after a major overhaul)
- introduction of things such as LED lighting (i.e. LED lights give off less heat so boiler has to produce more).
There were 1037 heating degree days in (year after) whereas only 1017 heating degree days in (year before) - however this difference was small. A few sites were removed from the results where LED lighting had gone in and there had been a significant change to the running conditions.
The fuel efficiency increase from 0.77 kW heat/fuel to 0.82 kW heat/fuel.
An improvement of 6%.
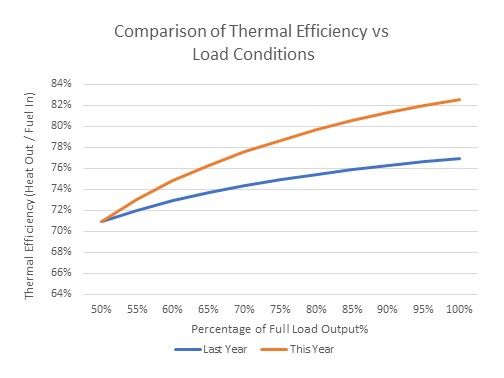
Measurements also showed that thermal efficiency (heat out / fuel in) was not linear with load and that the Biomass boilers became more efficient the more heavily they were loaded.
Theoretically the boilers are 0% efficient at around 10% of full load, increasing to 55% at 30% of full load and 71% at 50% load. The results with and without additive only really started to diverge above 50% of full load.
The conclusion was that at an improvement of 6% the project had met its objectives.